5 Tips for “Spring Cleaning” Your Auto Repair Shop Inventory
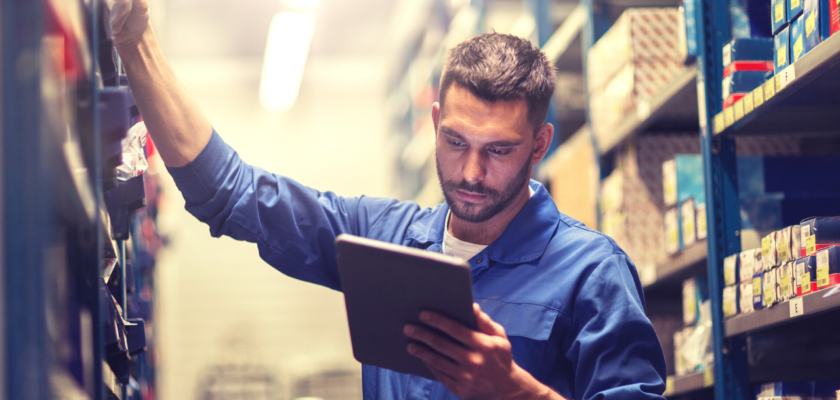
With the arrival of warmer weather and blooming trees, this new season also brings an opportunity for spring cleaning, in homes and businesses alike. As an auto repair shop owner, you may be looking for ways to straighten out your inventory as you move into springtime, and we’re here to help you get started.
Why auto repair shop inventory management?
Simply put, inventory is money. If you don’t know which parts you have in storage, you might find your capital disappearing without a record to explain why. Many auto repair shop owners take a reactive approach to their inventory management by only ordering parts on an as-needed basis or taking vague guesses at what they may need in the future. A reactive approach to inventory management also manifests as disorganization throughout the shop.
Reactive approaches can lead to loss of profits, as well as a slowdown of productivity (do you really want your staff to clock extra hours spent on a “scavenger hunt” for the right part in messy storage areas?)
Needless to say, auto repair shop inventory management enables shop owners to understand where their resources are going and stay on top of which parts they need to restock. It’s a great way to keep track of capital, speed up repairs, and provide overall better service for customers.
Defining Terms: The Difference Between Inventory and Stock
It’s important to note that there’s a difference between inventory and stock. They aren’t interchangeable terms. Inventory entails all items used by your shop, including parts put into customers’ cars and tools used by technicians. Stock only includes the parts that customers actually drive away with inside their cars. So, all stock is inventory, but not all inventory is stock.
This distinction highlights that auto repair shop inventory management best practices require us to keep track of the parts that get installed into customers’ cars and also keep a record of the tools used by shop staff.
Top 5 Best Practices for Auto Repair Shop Inventory Management
-
Take the time to organize and count all of your inventory to create a baseline.
Are all of your storage areas neat and easy to navigate? It’s difficult to move forward with auto repair shop inventory management if your spaces are messy and disorganized. Create a baseline of where everything should go and how much of each item you currently own. This practice will make it as simple as possible for your technicians to follow guidelines for inventory management. And speaking of inventory management guidelines…
-
Establish clear guidelines for all staff members to follow.
When do each of the items need to be restocked? Is there a baseline amount of an item that should get reordered each month because it’s used frequently, or does a specific item only need to be ordered on an as-needed basis? To establish your auto repair shop inventory management, all of these questions need to be answered with clear guidelines.
-
Delegate properly to staff members.
As a shop owner, you can’t be around all the time to enforce the guidelines for auto repair shop inventory management. Find ways for technicians to hold each other accountable and report which inventory they’re using on repairs each day. Keeping a log is a great place to start.
In addition, it’s important to put parameters around who gets to order certain parts. Some parts will be cheap and easy to order, while others are more specialized and expensive. Limit who gets to order the higher-priced parts to create a restocking system based around which technicians have more reliability and/or experience.
-
Regularly perform an inventory check.
Schedule inventory checks on a regular basis to stay updated on what spending looks like, and which items seem to be going faster or slower. Then, you can adjust accordingly in the weeks to come.
Using a quick formula called the inventory turnover ratio will provide you with useful information.
It is calculated as:
Inventory Turnover= Cost of Goods Sold/Average Inventory
Ideally, you should obtain this number once a month to maintain excellent auto repair shop inventory management.
-
Consider using software for inventory management
It’s possible that this list might seem overwhelming to you. We’ve essentially recommended that you organize and count your inventory, train your staff on new guidelines, gain an understanding of which items move off the shelves quicker or slower than others, etc.
With all of this in mind, many auto shop owners find the best way to manage auto repair shop inventory is to introduce software into their process.
R.O. Writer provides a specialized solution for auto repair shop inventory management. Our software includes features that enable you to:
-
Automate and manage purchase orders
The Inventory Management feature includes built-in pricing tools to control up to 5 price levels per part. Purchase Orders can be built automatically based on your stocking levels, and then electronically transmitted to your suppliers.
-
Track returns and cores plus quickly transfer parts between stores
The Inventory Module also includes core tracking from part purchase to core credit return. Multi-store owners can use the transfer feature to move parts between stores.
-
See all your inventory in one place
Over 20 built-in reports are included to track low stock, overstock, part usage, part audit trails, and inventory cycle counts. You can also create custom reporting views.
Ready to learn more about our Inventory Management software? Contact us at sales@rowriter.com.